What is wear-resistant casting and how does it work?
Do Cylpebs Grinding Media Increase Throughput?
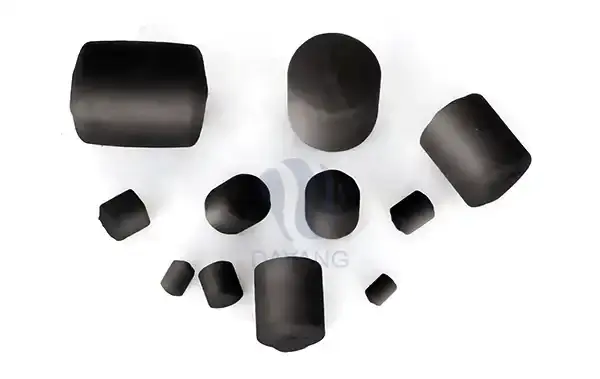
Grinding Cylpebs media are essential components in the efficiency and cost-effectiveness of grinding processes across various industries. These media, which come in different shapes and compositions, play a pivotal role in breaking down materials into finer particles. Among the numerous options available, cylpebs grinding media stand out due to their unique cylindrical shape and specific composition. This distinct form can significantly influence the throughput and overall performance of the grinding process.
How Can Grinding Balls Contribute to Sustainable Mining Practices?
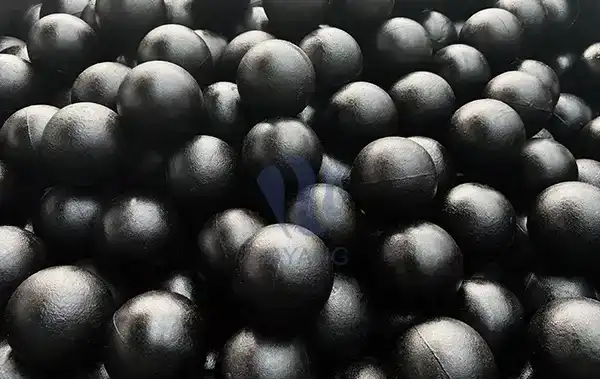
Determining the ideal grinding ball size is pivotal in augmenting the productivity and viability of grinding processes across different enterprises. The decision of ball size straightforwardly influences the grinding proficiency, molecule size appropriation, and generally performance of the processing activity.
How to Test Grinding Balls?
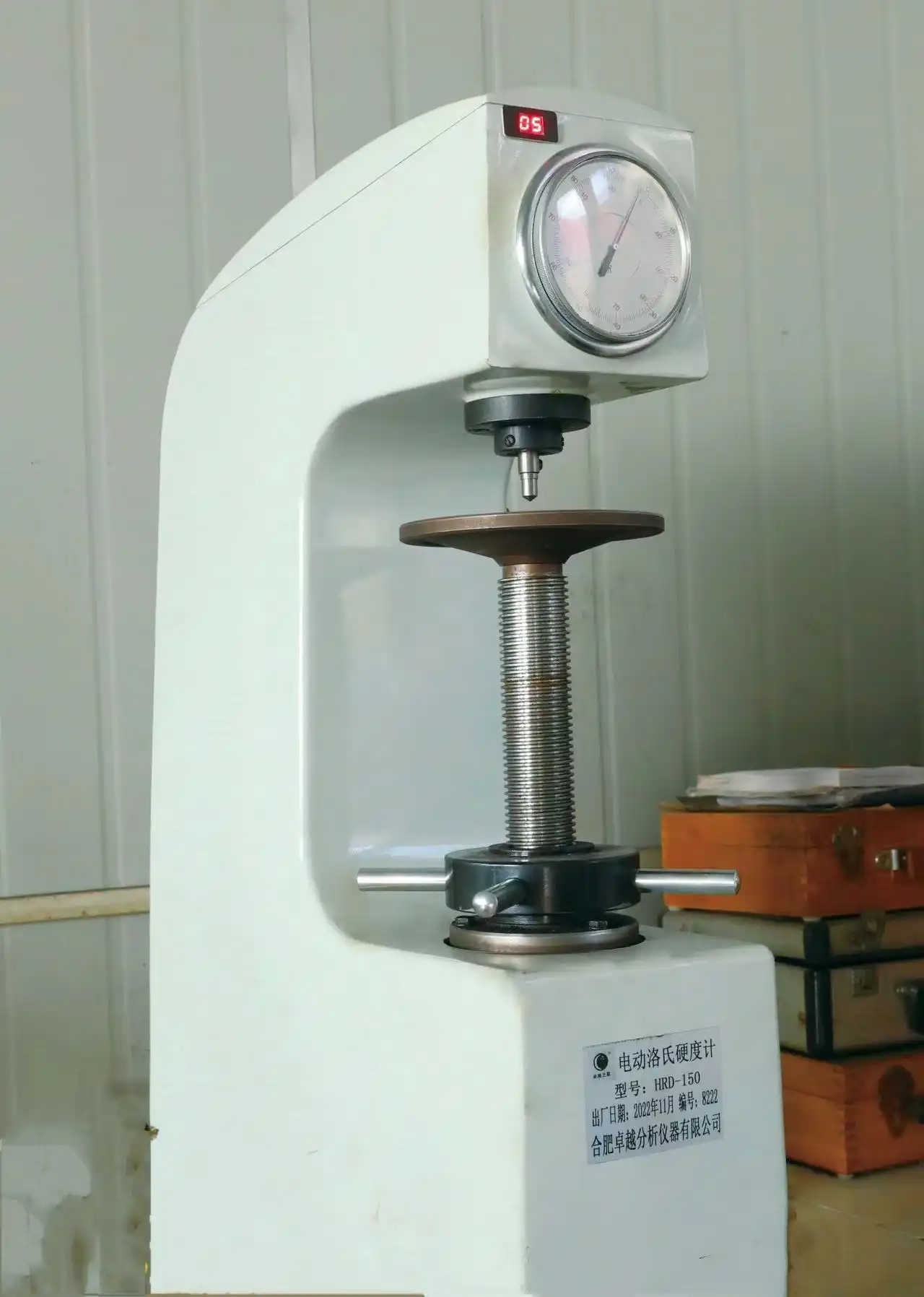
Grinding Ball are fundamental parts utilized in different businesses, including mining, concrete plants, power stations, from there, the sky is the limit. Guaranteeing their quality and execution is significant to upgrading tasks and accomplishing wanted results. This article provides insights into the durability, effectiveness, and overall quality of grinding balls by examining efficient testing techniques.
Can grinding balls be used for both wet and dry milling?
Grinding balls are essential components in ball milling operations, crucial for pulverizing materials into fine particles in both wet and dry conditions. Understanding their versatility is key to optimizing milling processes for various applications. Grinding balls play a vital role in the process of ball milling, which is widely used in various industries for the production of powders and materials. Whether in wet or dry milling applications, these spheres are capable of effectively reducing the size of particles, enhancing mixing processes, and facilitating chemical reactions.
How are high chrome grinding balls produced?
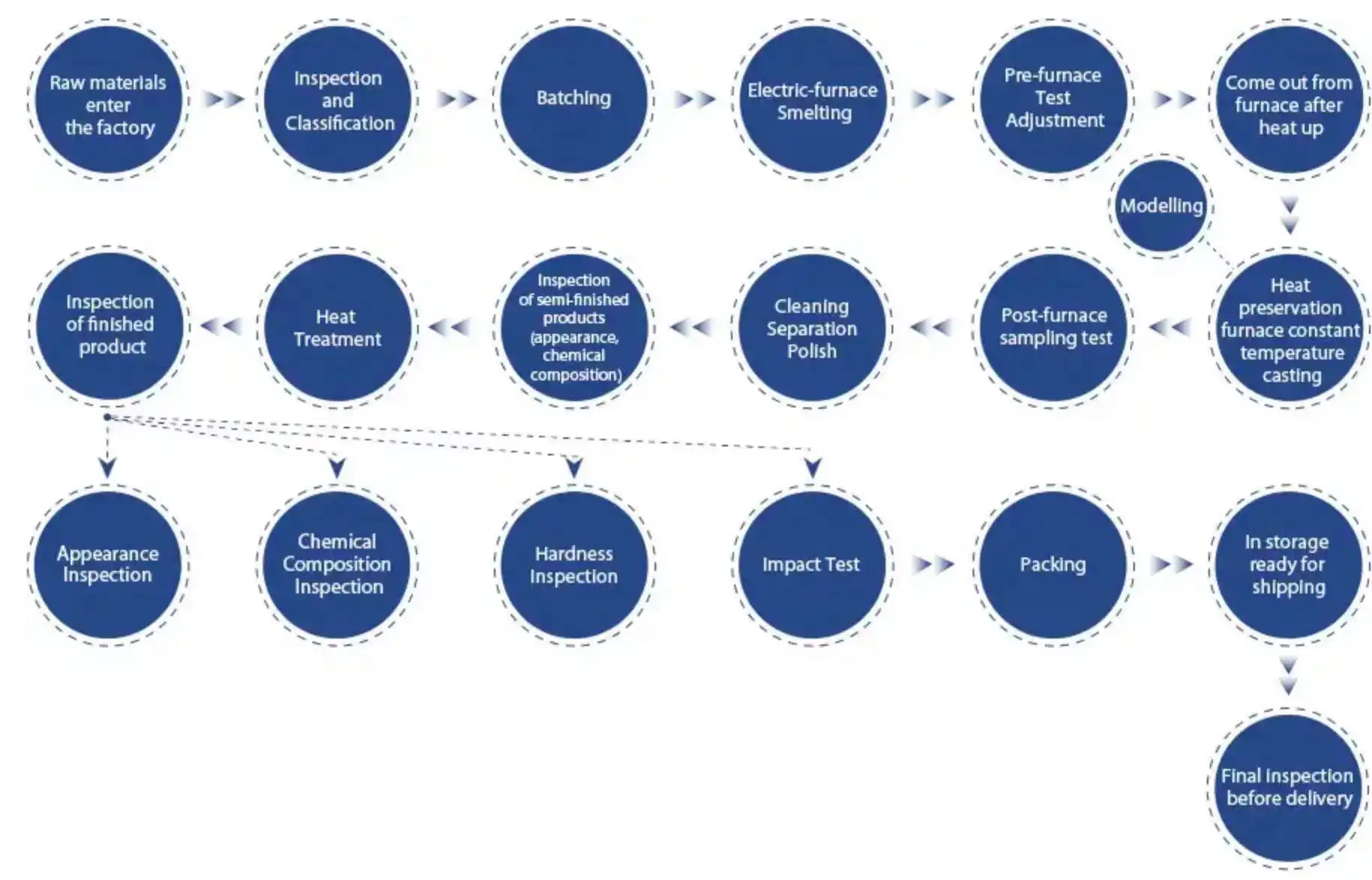
In the world of industrial grinding, high chrome grinding balls play a crucial role in enhancing efficiency and durability. These robust spheres are essential components in various industries, including cement production, mining, and power generation. But have you ever wondered about the intricate process behind their creation? Let's delve into the fascinating world of high chrome grinding ball production and uncover the secrets behind their exceptional performance.
What factors influence the quality of casting grinding balls?

In the world of industrial grinding, casting grinding balls play a crucial role in various sectors, including cement production, mining, and power generation. These spherical metallic tools are essential for breaking down materials into fine particles, and their quality can significantly impact the efficiency and effectiveness of grinding operations. Understanding the factors that influence the quality of casting grinding balls is vital for manufacturers and end-users alike. Let's delve into the key elements that determine the performance and durability of these indispensable grinding media.
The Ultimate Guide to Milling Balls
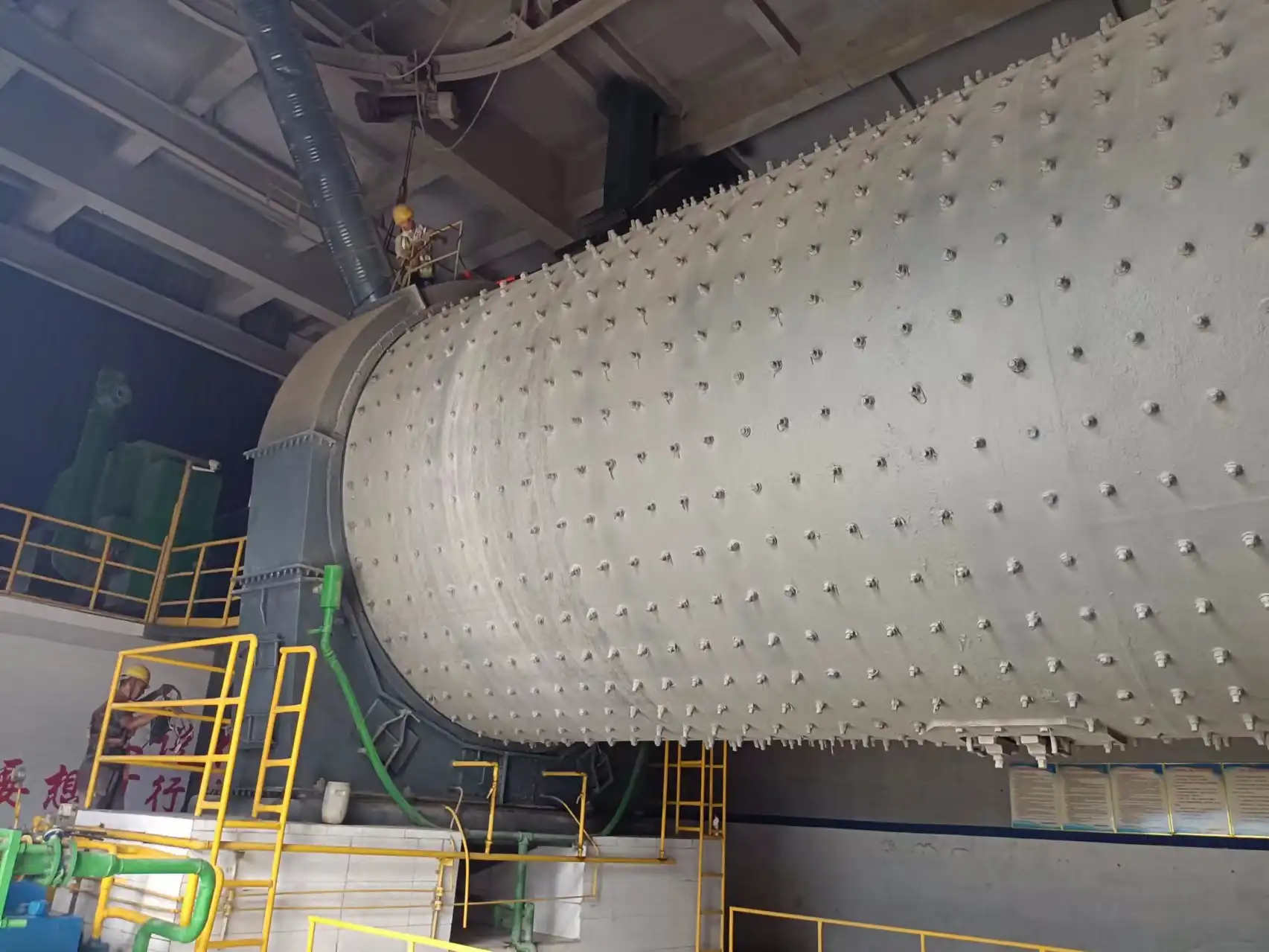
In the world of industrial grinding and material processing, milling balls play a crucial role in achieving optimal results. These small but mighty spheres are the unsung heroes of numerous industries, from mining to pharmaceuticals. This comprehensive guide will delve into the intricacies of milling balls, their applications, and how to choose the right ones for your specific needs.
What innovations are being made in grinding ball technology for mining?
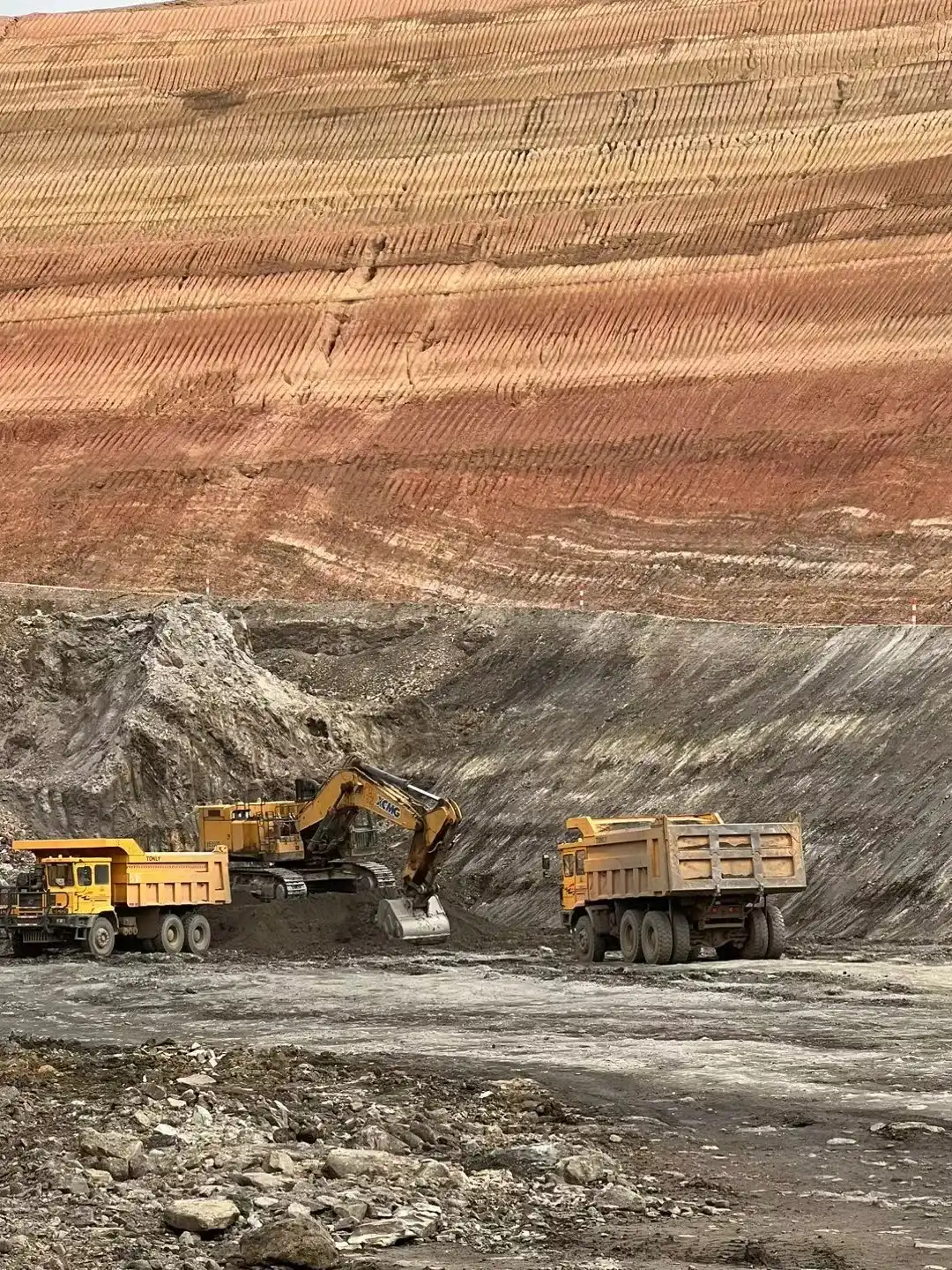
Grinding balls for mining have undergone significant technological advancements in recent years, revolutionizing the mineral processing industry. These innovations aim to enhance efficiency, durability, and performance while reducing operational costs. Some of the key developments include the introduction of high-chromium alloys, which offer superior wear resistance and longer service life. Additionally, manufacturers are experimenting with novel shapes and sizes, such as oval or cylindrical grinding media, to optimize grinding efficiency. Advanced manufacturing techniques, like powder metallurgy and precision casting, are being employed to produce grinding balls with improved microstructure and consistent quality. Moreover, smart coating technologies are being developed to further enhance the wear resistance and reduce contamination in the grinding process. These innovations collectively contribute to increased productivity, reduced energy consumption, and improved overall performance in mining operations.
What are high chrome steel grinding media balls?
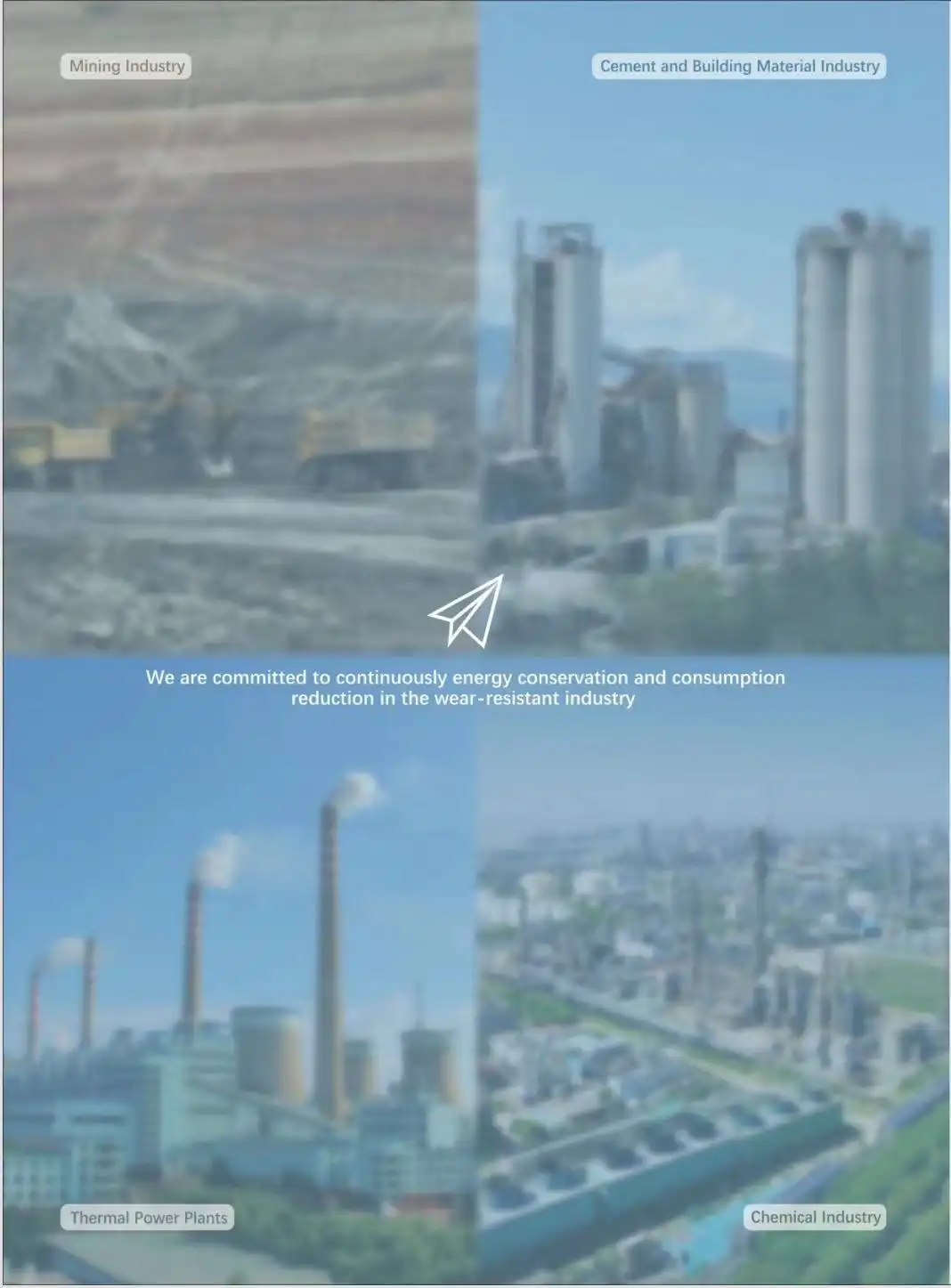
High chrome steel grinding media balls are essential components in various industrial processes, particularly in the mining, cement, and power generation sectors. These specialized balls are designed to withstand extreme wear and tear while efficiently grinding materials into fine particles. In this comprehensive guide, we'll explore the characteristics, applications, and benefits of high chrome steel grinding media balls, shedding light on their crucial role in modern industrial operations.
High chrome grinding media balls: A Comprehensive Guide

In the world of mineral processing, grinding media balls play a crucial role in reducing the size of materials and liberating valuable minerals. This comprehensive guide will delve into the intricacies of high chrome grinding media balls, exploring their functions, materials, and benefits in mineral processing operations. Whether you're in the mining, cement, or chemical industry, understanding the importance of high-quality grinding media is essential for optimizing your operations.
What are the economic implications of ball mill media wear rate?
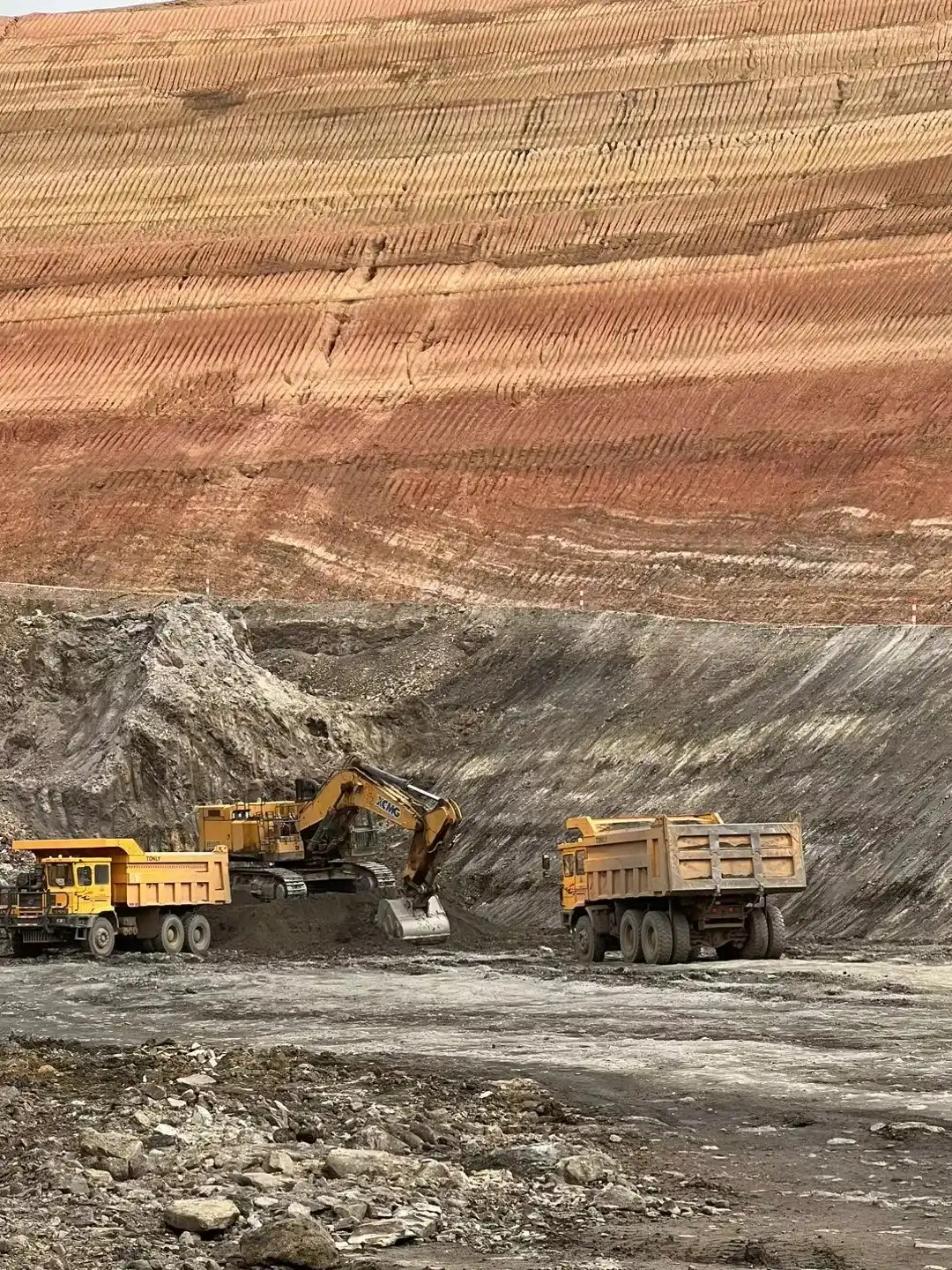
In the world of industrial grinding, the wear rate of ball mill media plays a crucial role in determining operational efficiency and cost-effectiveness. As a leading manufacturer of high-quality grinding media, NINGHU understands the significance of this factor in the overall economic landscape of various industries. This article delves into the economic implications of ball mill media wear rate, exploring how it affects total cost of ownership, long-term value, and return on investment.