Role of Grinding Balls in Mineral Processing
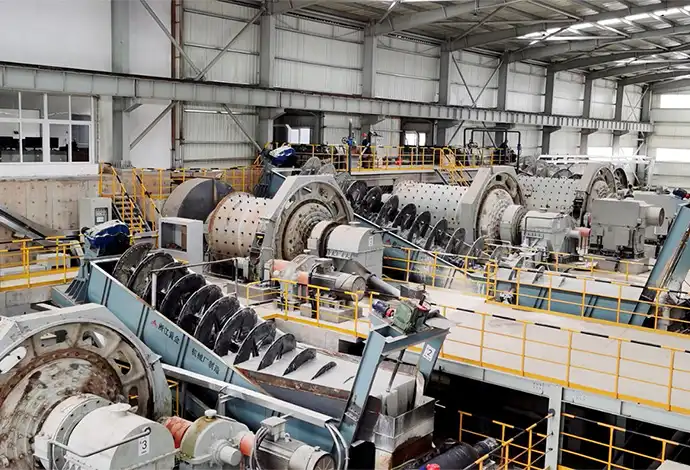
In the domain of mineral handling, the part of crushing balls is vital. As a crucial component in the comminution handle, Grinding media encourage the pulverizing and pounding of metal particles, empowering proficient extraction of important minerals. In this article, we dive into the multifaceted centrality of pounding balls in mineral preparing, investigating their capacities, sorts, and significance in optimizing mineral handling operations.
Why Choose Cylpebs Grinding Media?
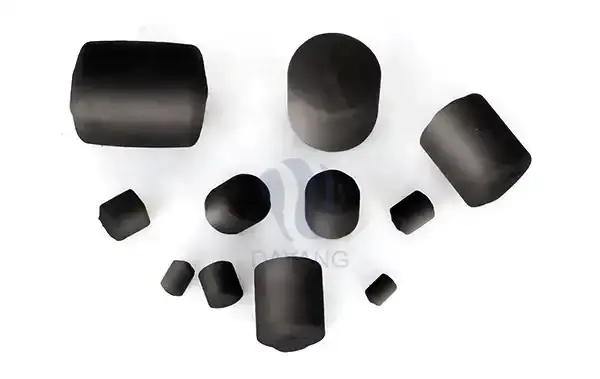
Cylpebs grinding media offer unique advantages over conventional ball or rod-shaped media that can improve the efficiency and cost-effectiveness of a variety of grinding applications. Cylpebs are an alternative to the more typical spherical or rod-like grinding mediums because of their cylindrical shape. As a result of this particular calculation, they are an important option for getting the best crushing results under certain conditions. Let's take a closer look at the reasons why Cylpebs grinding media might be the best choice for your grinding needs.
How to Store Grinding Balls?
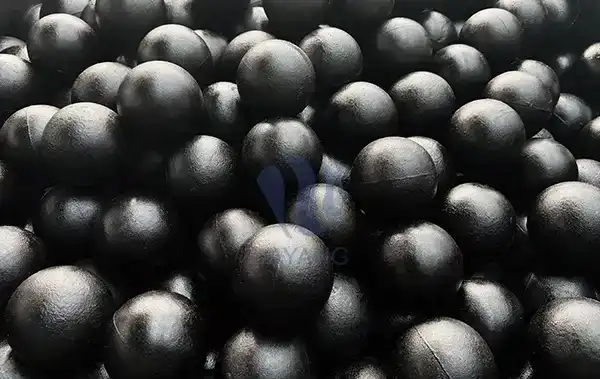
Putting away Grinding Ball appropriately is urgent for keeping up with their quality and viability in modern activities. Whether ceramic balls used in chemical processing or steel balls used in mining, proper storage ensures their performance and longevity. This article looks at the best ways to store grinding balls to make sure they last as long as possible and work as well.
Grinding Balls: Vital for Cement Industries
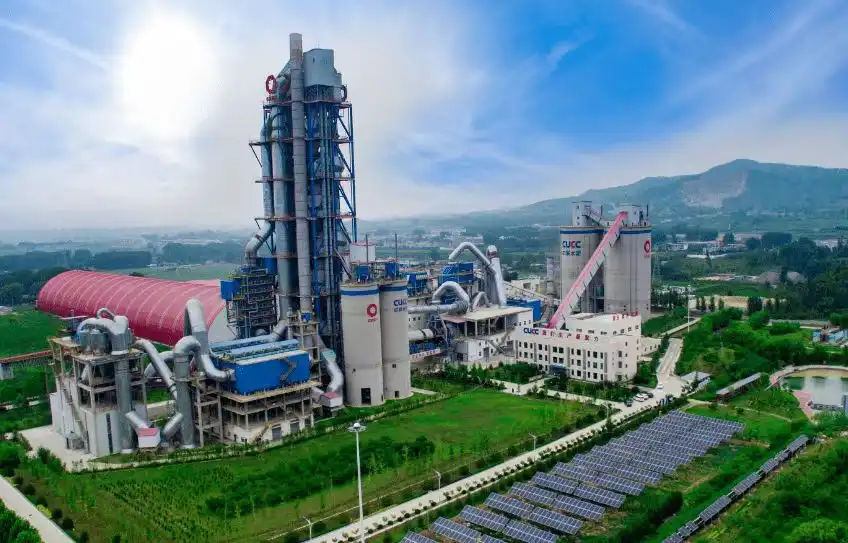
Grinding Balls play a pivotal part in the cement industry, where they are utilized to smash and crush crude materials into a fine powder. These balls are regularly made from different materials such as steel, press, ceramic, or indeed elastic, depending on the application and necessities of the cement fabricating handle. In this article, we will dig into the significance of pounding balls in cement generation and investigate their different employments and functionalities inside the industry.
How to Replace Grinding Balls?
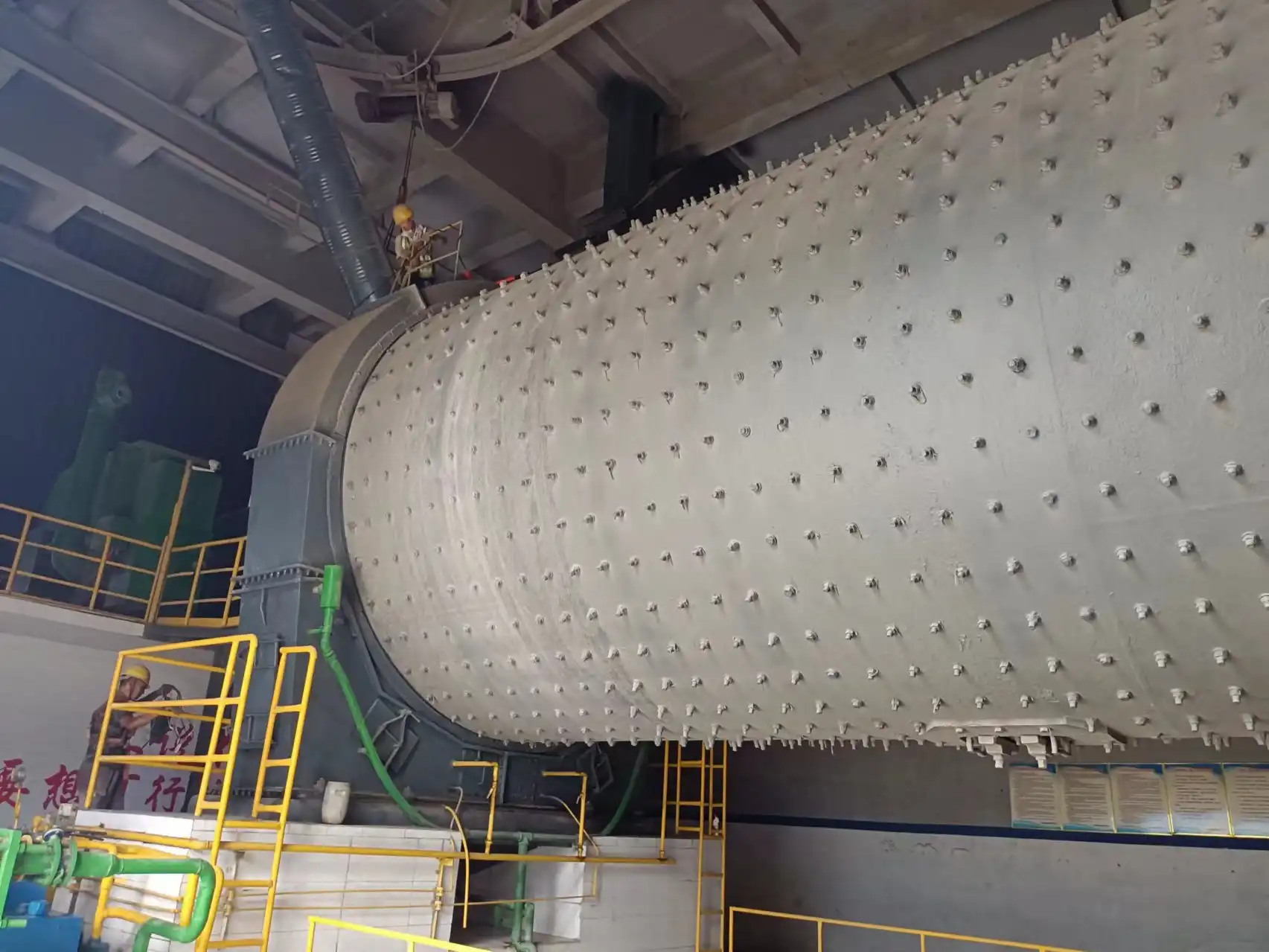
It is essential to change the Grinding Ball in a mill so that the material is effectively ground and the machine runs at its best. Grinding media maintenance and replacement are crucial to operational efficiency and cost-effectiveness in mining, mineral processing, or cement plants. This article investigates the fundamental stages and contemplations associated with supplanting crushing balls, resolving normal inquiries and giving pragmatic experiences accumulated from top assets in the field.
What are the most common sizes of grinding balls for different applications?
What are the typical applications of high chrome grinding balls in mining and cement?
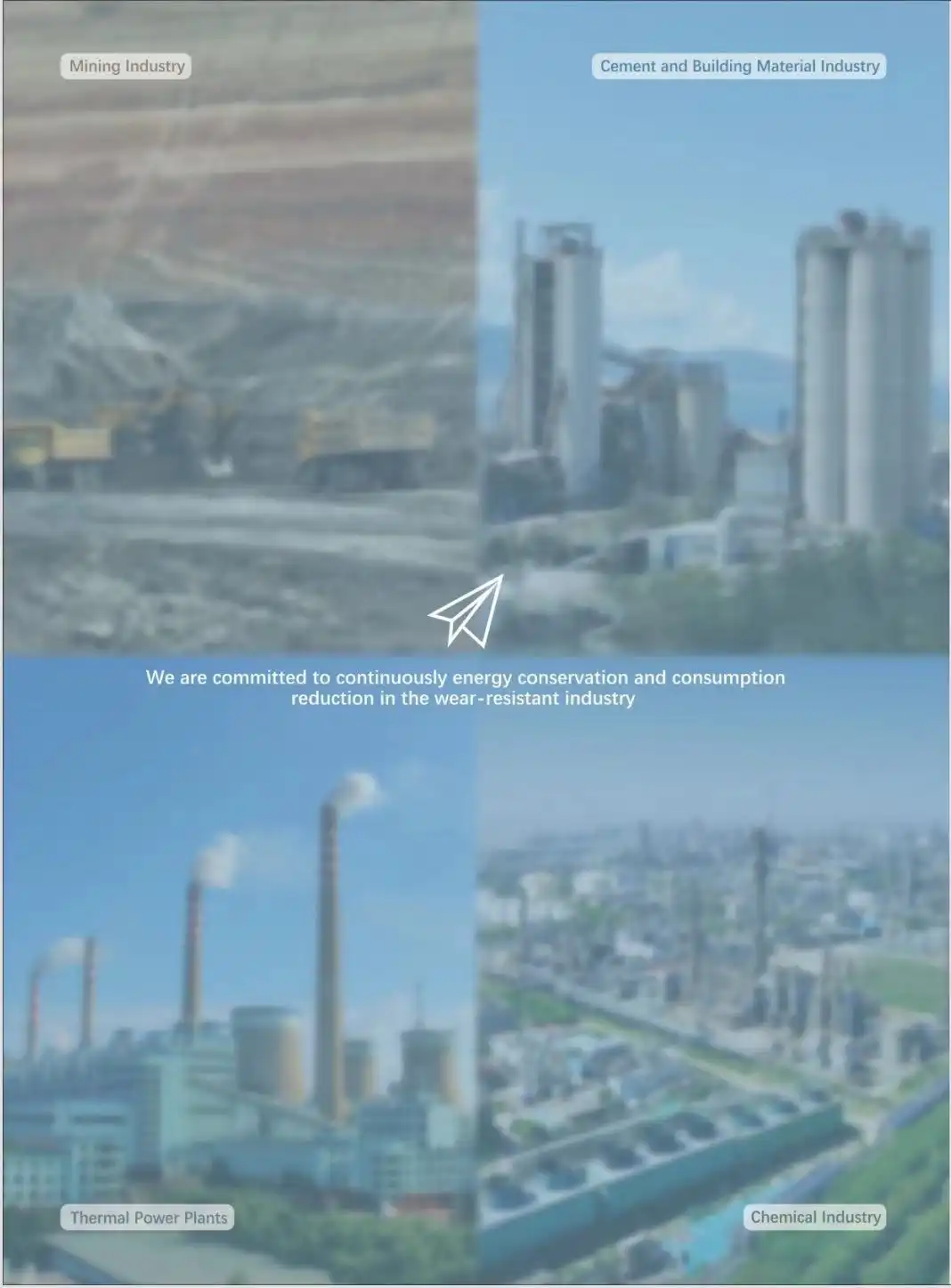
High chrome grinding balls are indispensable components in various industries, including cement production, mining, and power generation. These robust spheres play a crucial role in grinding and pulverizing materials, contributing significantly to the efficiency of industrial processes. To ensure optimal performance and longevity of it, proper cleaning and maintenance are paramount. This comprehensive guide will delve into the intricacies of caring for these essential industrial tools, providing valuable insights for professionals and enthusiasts alike.
5 Creative Ways to Use Grinding Balls
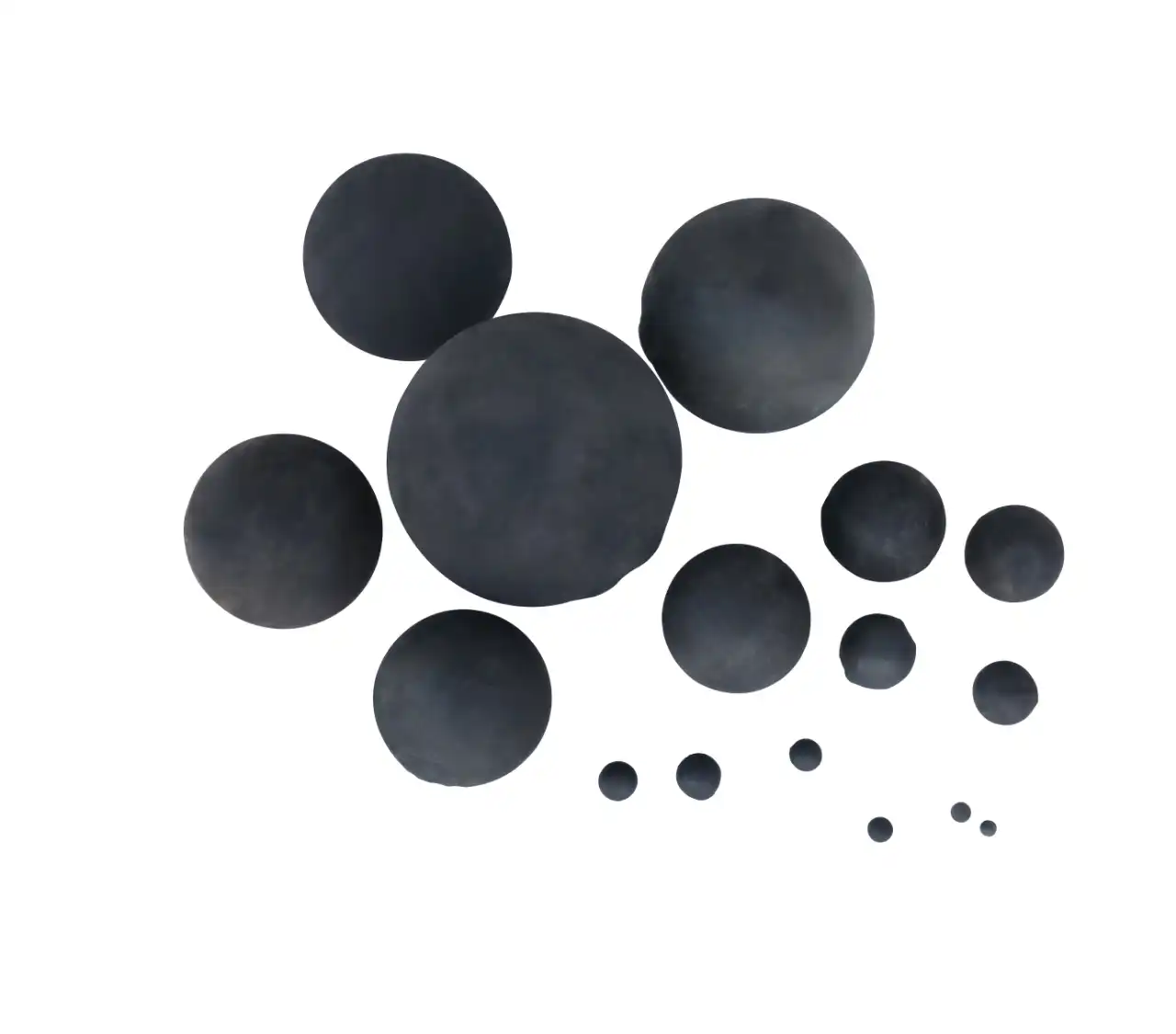
Grinding balls, particularly casting grinding balls, are essential components in various industrial processes. While their primary function is to crush and grind materials in mills, these versatile tools have found their way into some unexpected applications. In this article, we'll explore five creative ways to use grinding balls that you might not have considered before.
Environmental Impact of Milling Balls
.webp)
In the world of industrial grinding, milling balls play a crucial role in various sectors, including mining, cement manufacturing, and power generation. However, as our global focus shifts towards sustainability, it's essential to consider the environmental impact of these essential components. This article delves into eco-friendly options, waste reduction strategies, and responsible disposal methods for milling balls, offering valuable insights for industries seeking to minimize their ecological footprint.
The Future of high chrome grinding media balls in Industry
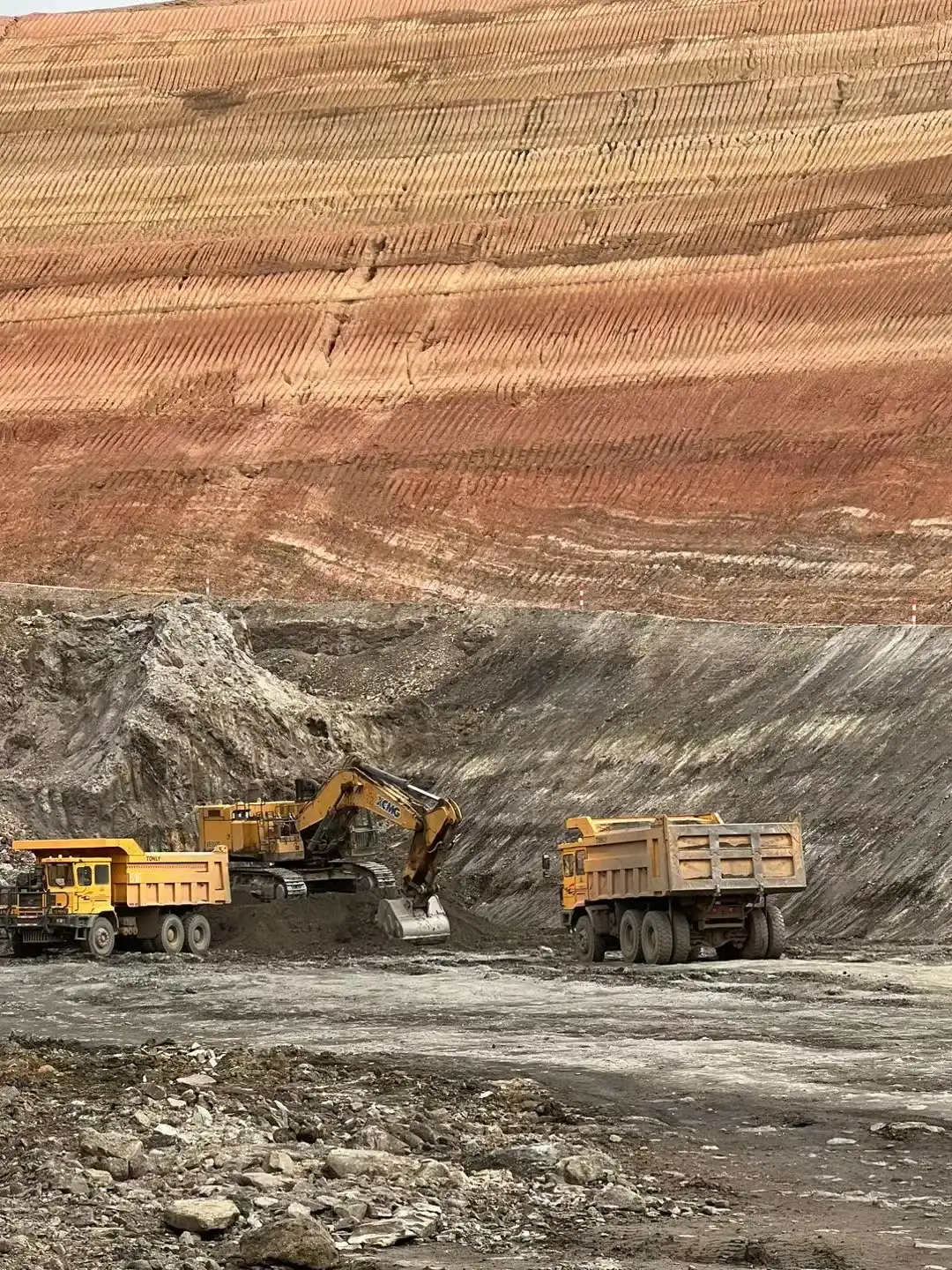
The mining and mineral processing industries are constantly evolving, and one area that's seeing significant advancements is the technology behind high chrome grinding media balls. These essential components play a crucial role in the mineral extraction process, and their future looks promising. In this article, we'll explore the latest innovations, environmental considerations, and how these advances are enhancing mineral extraction efficiency.
The Ultimate Guide to Grinding Media Steel Balls
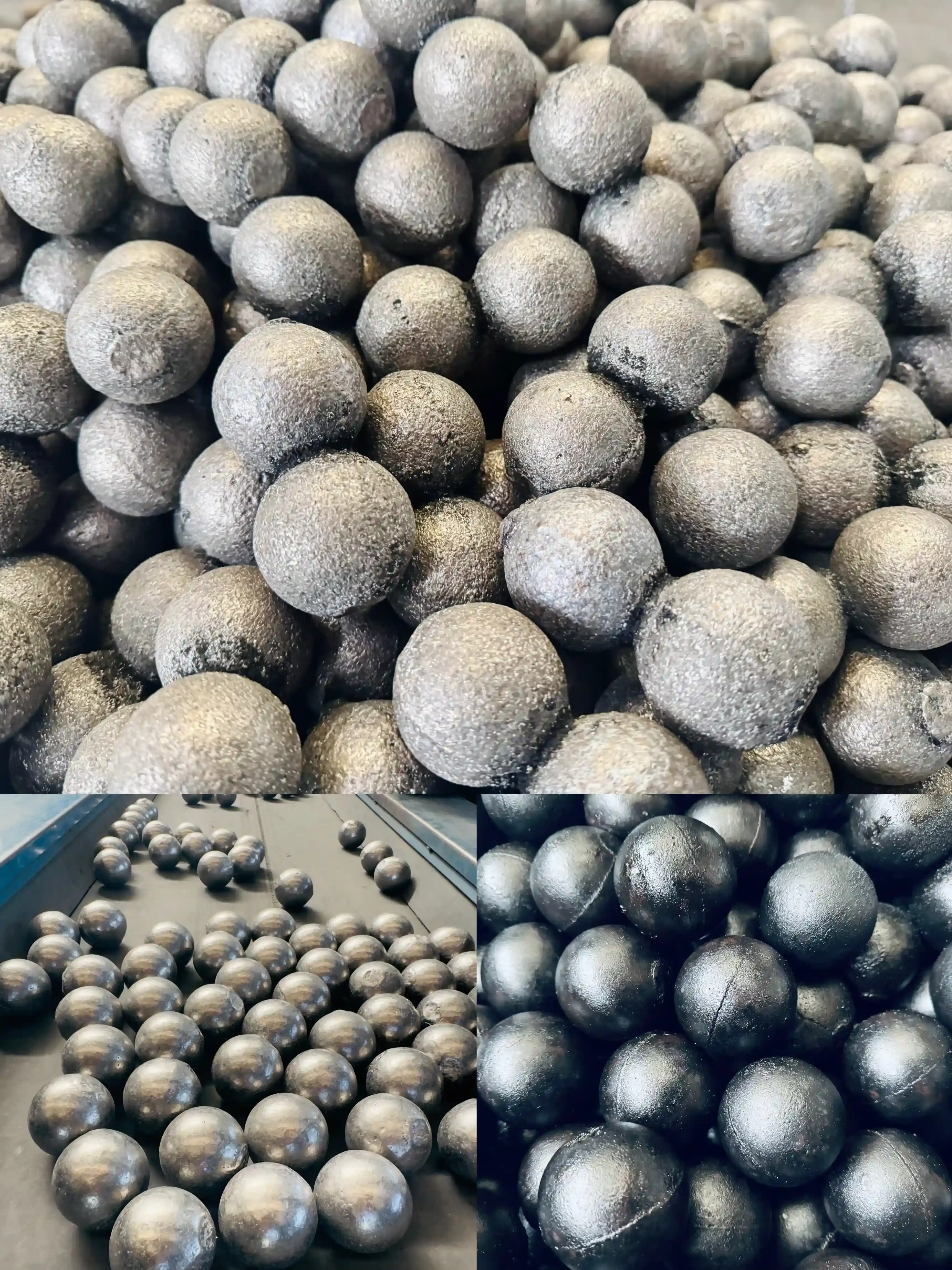
In the world of industrial processing, grinding media steel balls play a pivotal role in transforming raw materials into valuable resources. These unassuming spheres are the unsung heroes of industries ranging from mining to cement production, enabling efficient size reduction and material refinement. In this comprehensive guide, we'll delve into the intricate world of grinding media steel balls, exploring their nature, selection criteria, and the myriad benefits they offer to various industrial applications.
High chrome grinding media balls: Benefits & Uses
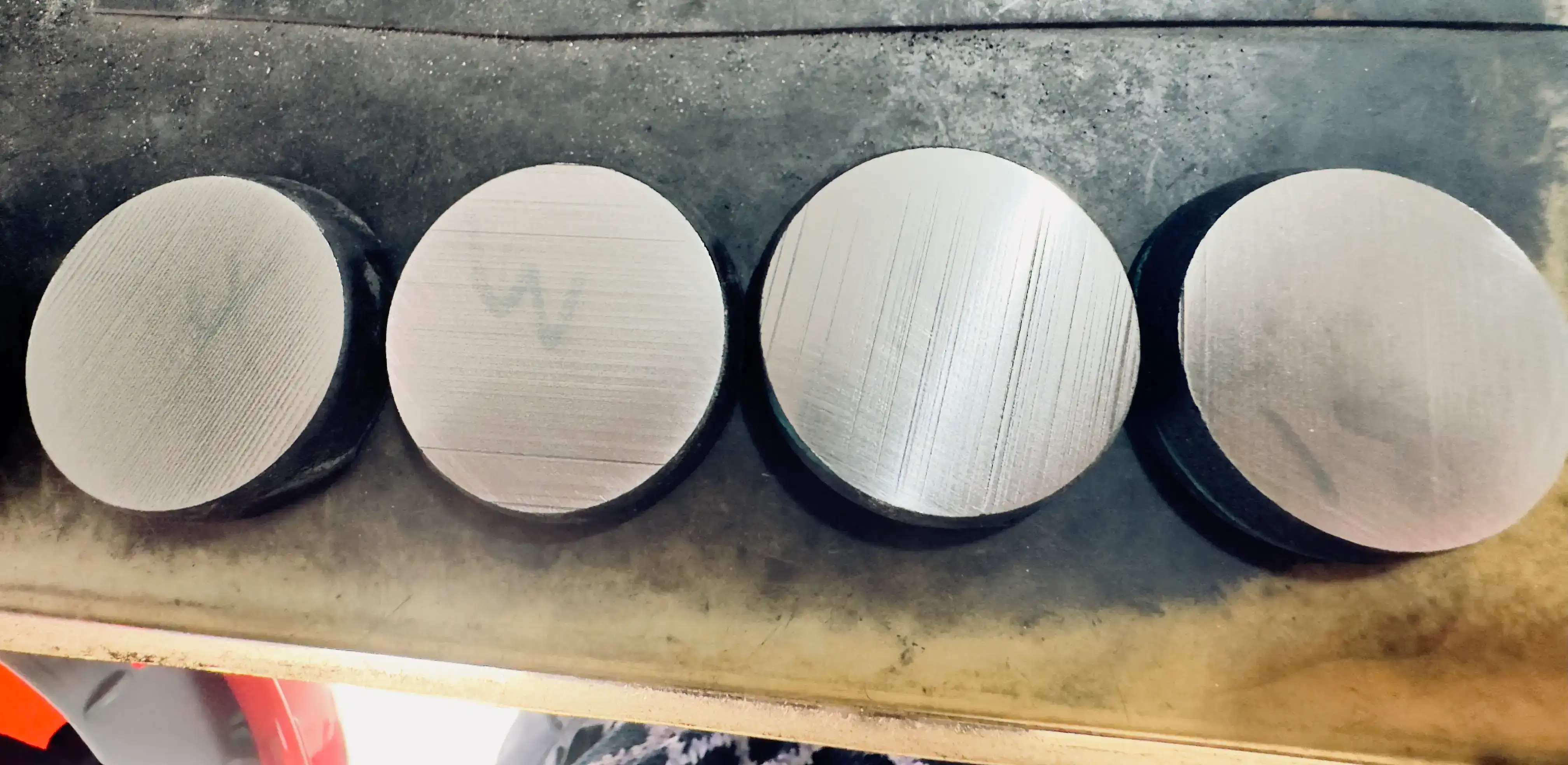
In the world of industrial grinding and milling, the choice of grinding media can significantly impact operational efficiency and product quality. Among the various options available, high chrome grinding media balls have emerged as a top choice for many industries. These robust spheres play a crucial role in the comminution process, breaking down materials into finer particles with impressive efficiency. Let's delve into the benefits and uses of these remarkable grinding tools.