Corrosion Resistance of Grinding Balls
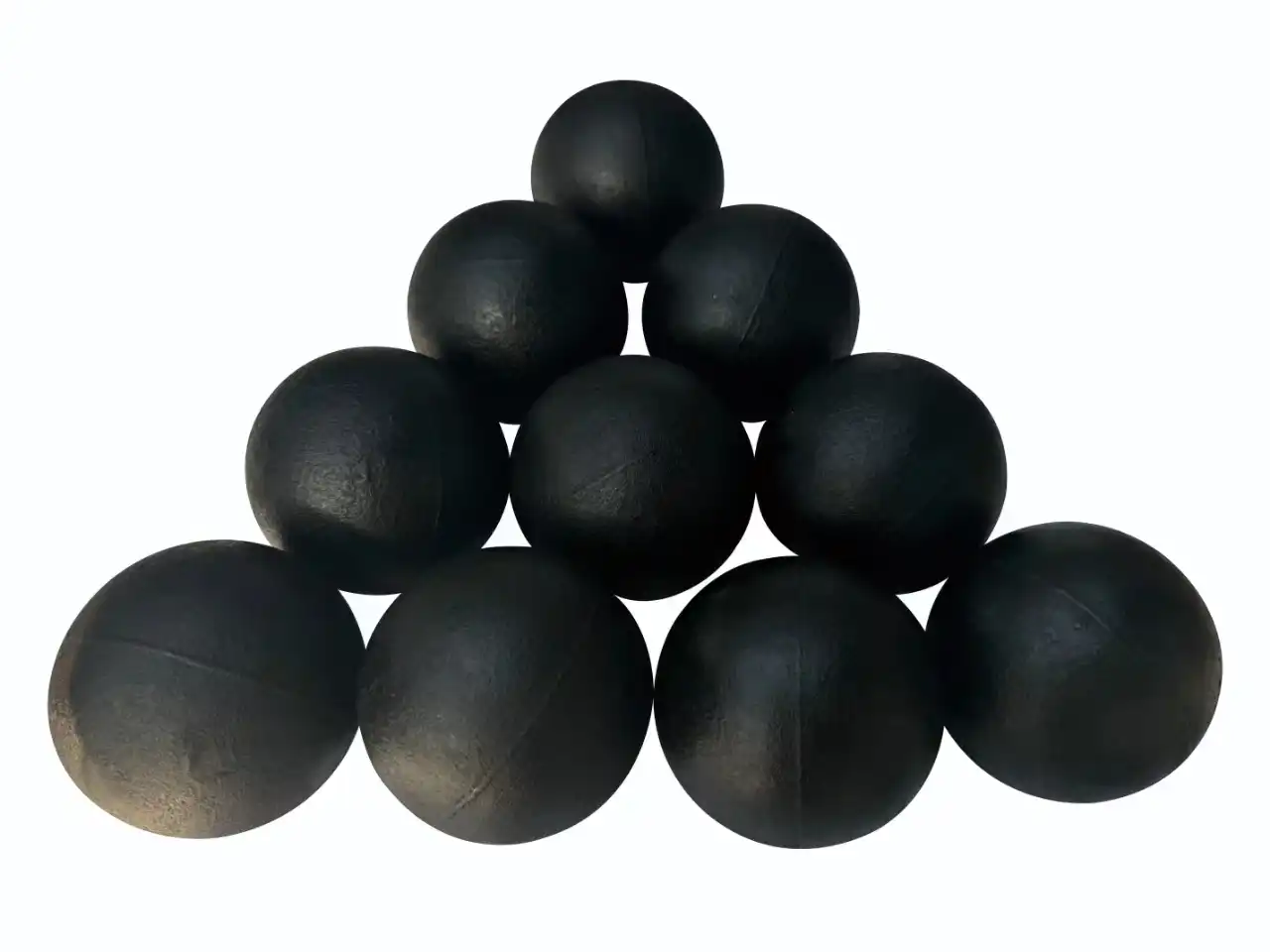
In the realm of industrial processes, the efficacy of grinding balls plays a pivotal role in ensuring the efficiency and longevity of various operations. Among the myriad factors influencing their performance, corrosion resistance stands out as a critical determinant. In this comprehensive exploration, we delve into the nuances of corrosion resistance concerning grinding balls. From understanding the fundamental components to down to earth suggestions, this talk points to prepare experts and devotees alike with priceless experiences into optimizing mechanical processes.
How do I choose grinding media?
Role of Grinding Balls in Mineral Processing
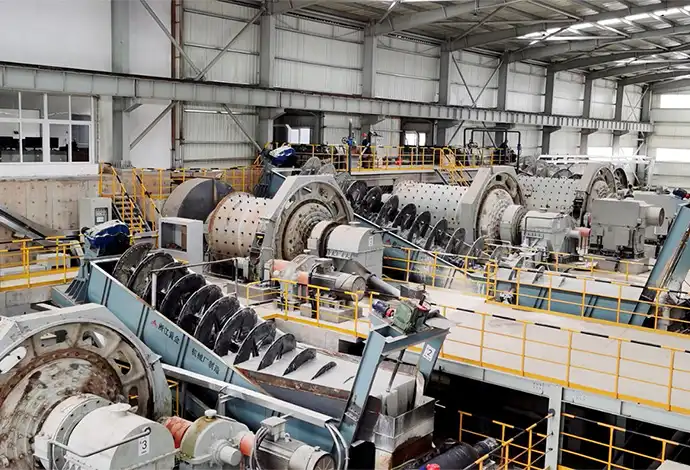
In the domain of mineral handling, the part of crushing balls is vital. As a crucial component in the comminution handle, Grinding media encourage the pulverizing and pounding of metal particles, empowering proficient extraction of important minerals. In this article, we dive into the multifaceted centrality of pounding balls in mineral preparing, investigating their capacities, sorts, and significance in optimizing mineral handling operations.
Why Choose Cylpebs Grinding Media?
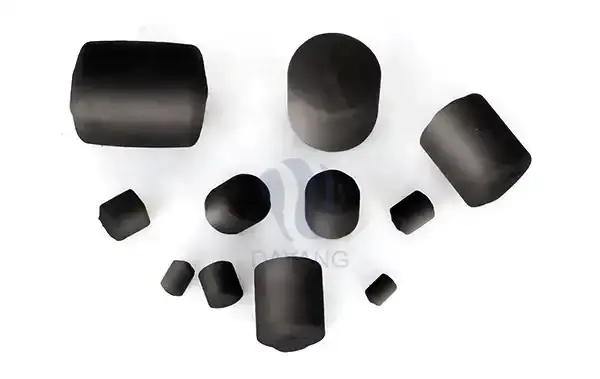
Cylpebs grinding media offer unique advantages over conventional ball or rod-shaped media that can improve the efficiency and cost-effectiveness of a variety of grinding applications. Cylpebs are an alternative to the more typical spherical or rod-like grinding mediums because of their cylindrical shape. As a result of this particular calculation, they are an important option for getting the best crushing results under certain conditions. Let's take a closer look at the reasons why Cylpebs grinding media might be the best choice for your grinding needs.
How to Store Grinding Balls?
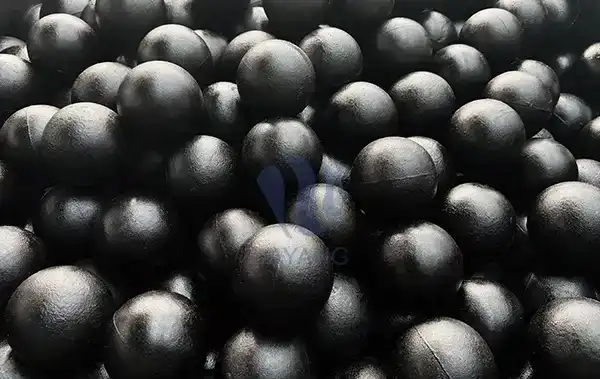
Putting away Grinding Ball appropriately is urgent for keeping up with their quality and viability in modern activities. Whether ceramic balls used in chemical processing or steel balls used in mining, proper storage ensures their performance and longevity. This article looks at the best ways to store grinding balls to make sure they last as long as possible and work as well.
How does the shape of grinding balls affect milling efficiency?
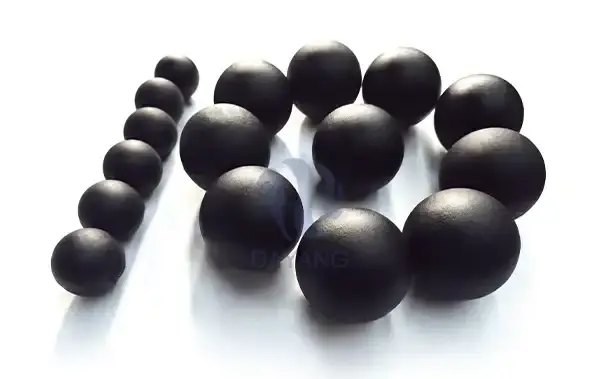
In the realm of industrial processes like milling and grinding, efficiency is paramount. The choice of grinding balls plays a significant role in determining milling efficiency and performance. From the material composition to the shape and size, each aspect can affect how materials are ground down and how efficiently the process is carried out.
How can you select the appropriate size of high chrome grinding balls for your application?
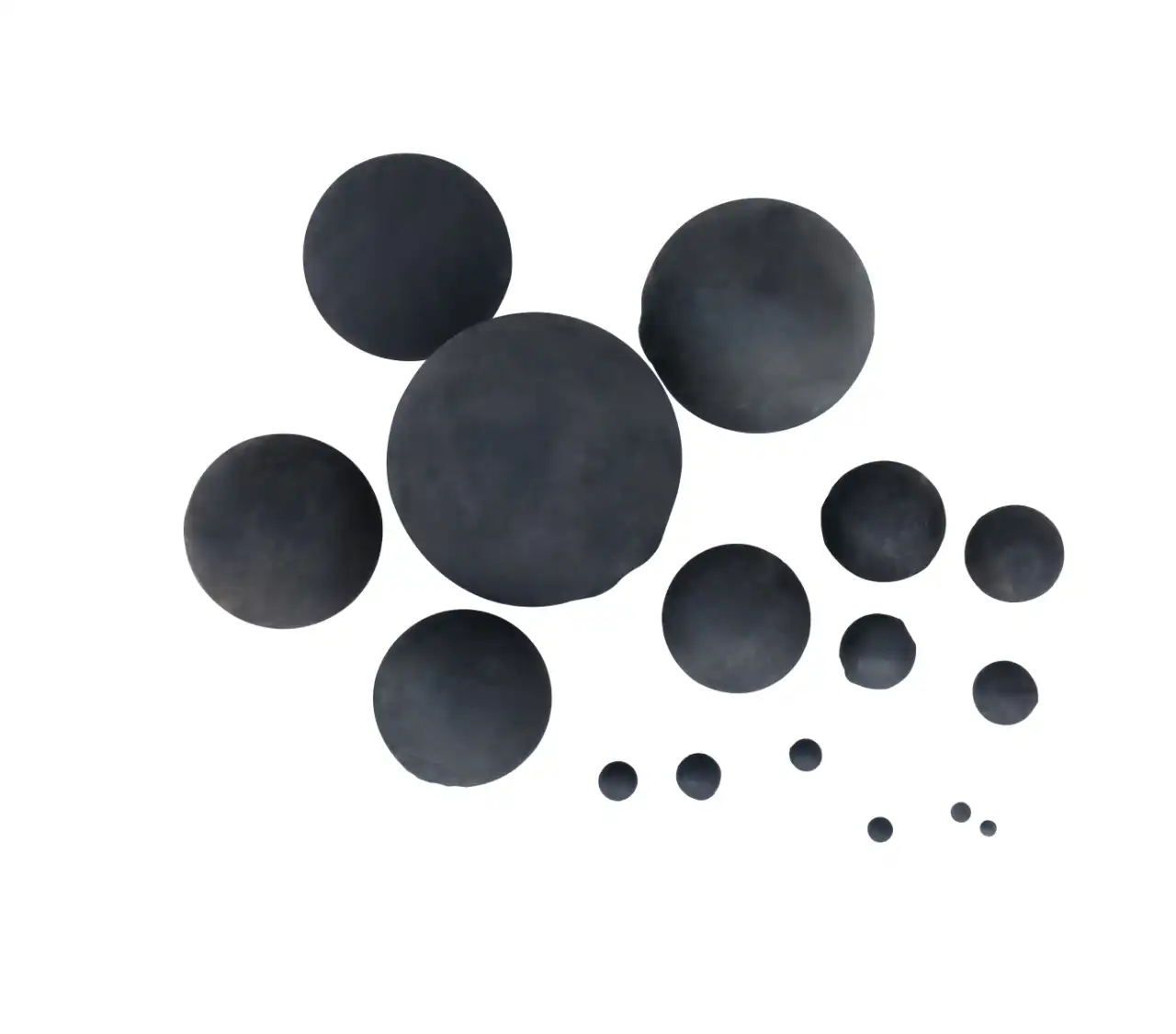
Selecting the right size of high chrome grinding balls is crucial for optimizing your grinding process. Whether you're in the cement, mining, or power generation industry, choosing the appropriate ball size can significantly impact your operation's efficiency and cost-effectiveness. This comprehensive guide will walk you through the key factors to consider when selecting high chrome grinding balls, ensuring you make an informed decision for your specific application.
How do I maintain casting grinding balls for optimal performance?
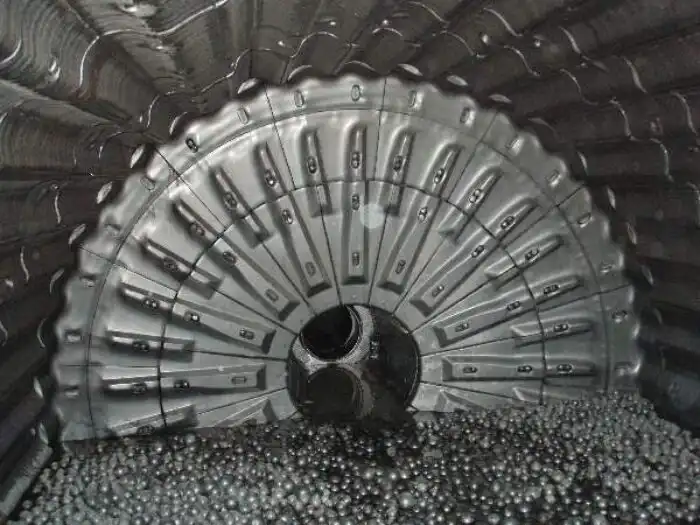
Casting grinding balls are indispensable components in various industries, including cement production, metallurgy, and mining. These robust spheres play a crucial role in pulverizing materials to achieve desired particle sizes. To ensure longevity and maintain peak performance, proper maintenance of it is essential. In this comprehensive guide, we'll explore effective strategies to keep your grinding media in top-notch condition, maximizing efficiency and minimizing downtime.
How to Replace Grinding Balls?
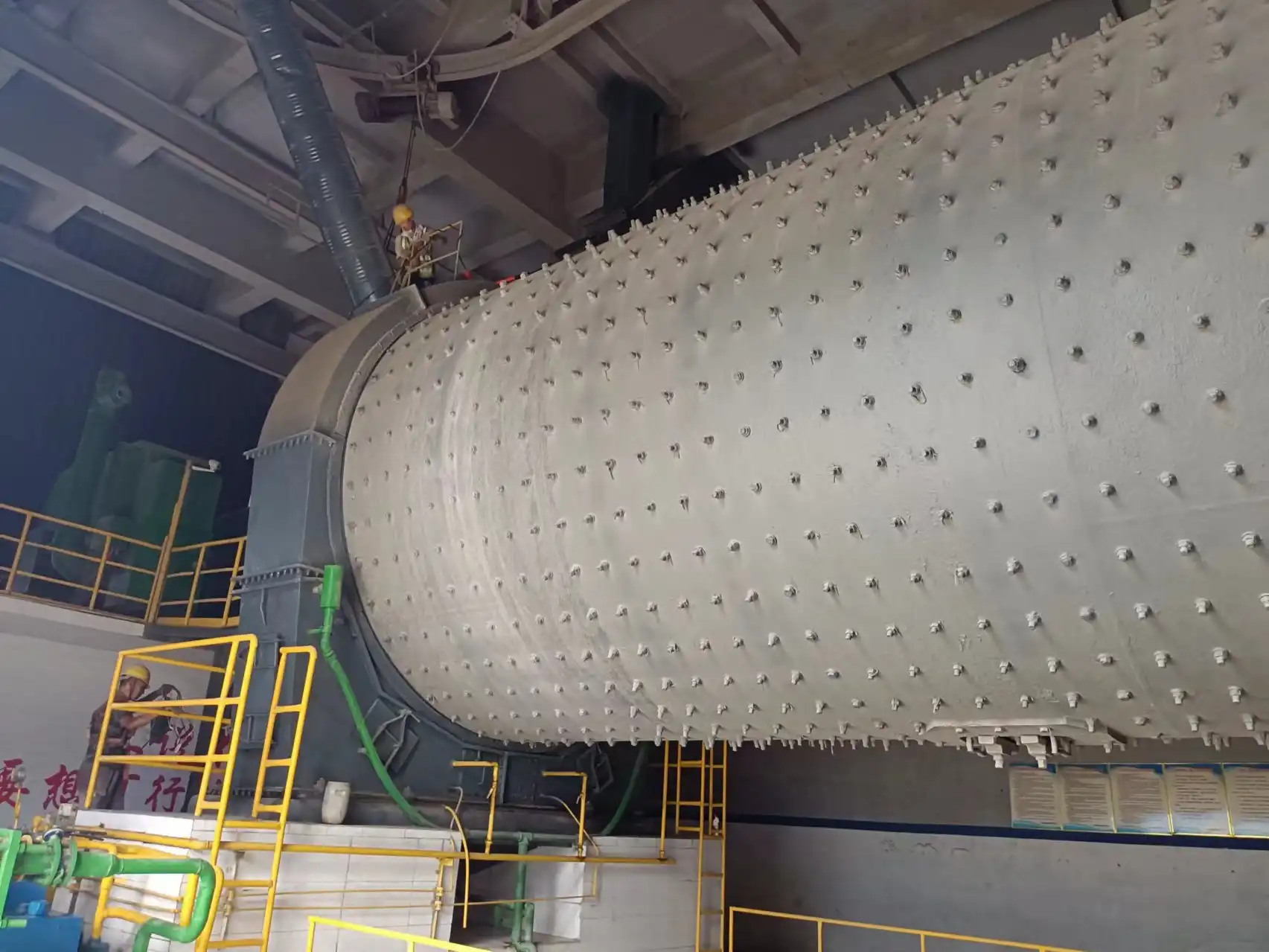
It is essential to change the Grinding Ball in a mill so that the material is effectively ground and the machine runs at its best. Grinding media maintenance and replacement are crucial to operational efficiency and cost-effectiveness in mining, mineral processing, or cement plants. This article investigates the fundamental stages and contemplations associated with supplanting crushing balls, resolving normal inquiries and giving pragmatic experiences accumulated from top assets in the field.
What are the most common sizes of grinding balls for different applications?
What are the typical applications of high chrome grinding balls in mining and cement?
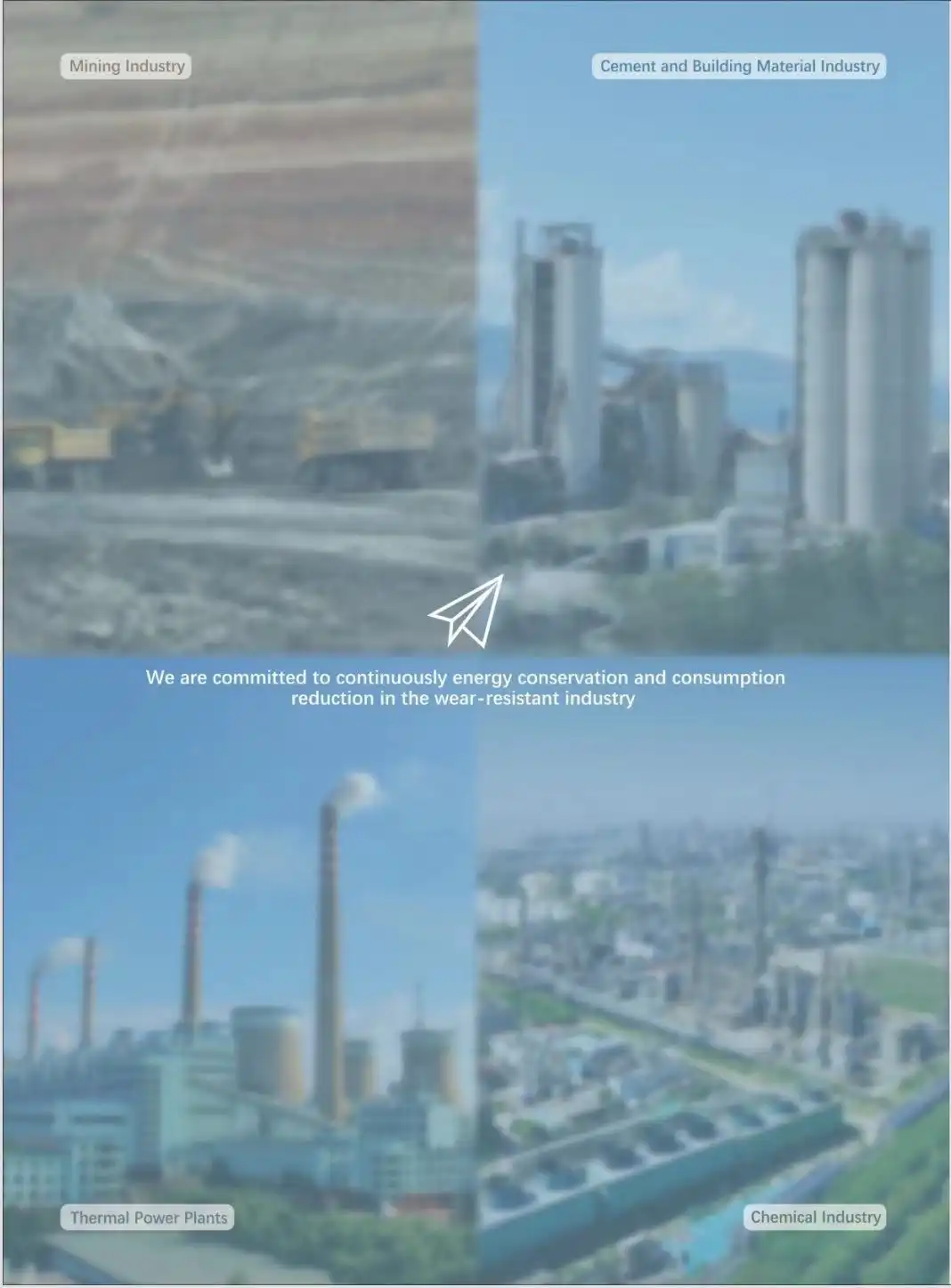
High chrome grinding balls are indispensable components in various industries, including cement production, mining, and power generation. These robust spheres play a crucial role in grinding and pulverizing materials, contributing significantly to the efficiency of industrial processes. To ensure optimal performance and longevity of it, proper cleaning and maintenance are paramount. This comprehensive guide will delve into the intricacies of caring for these essential industrial tools, providing valuable insights for professionals and enthusiasts alike.
5 Creative Ways to Use Grinding Balls
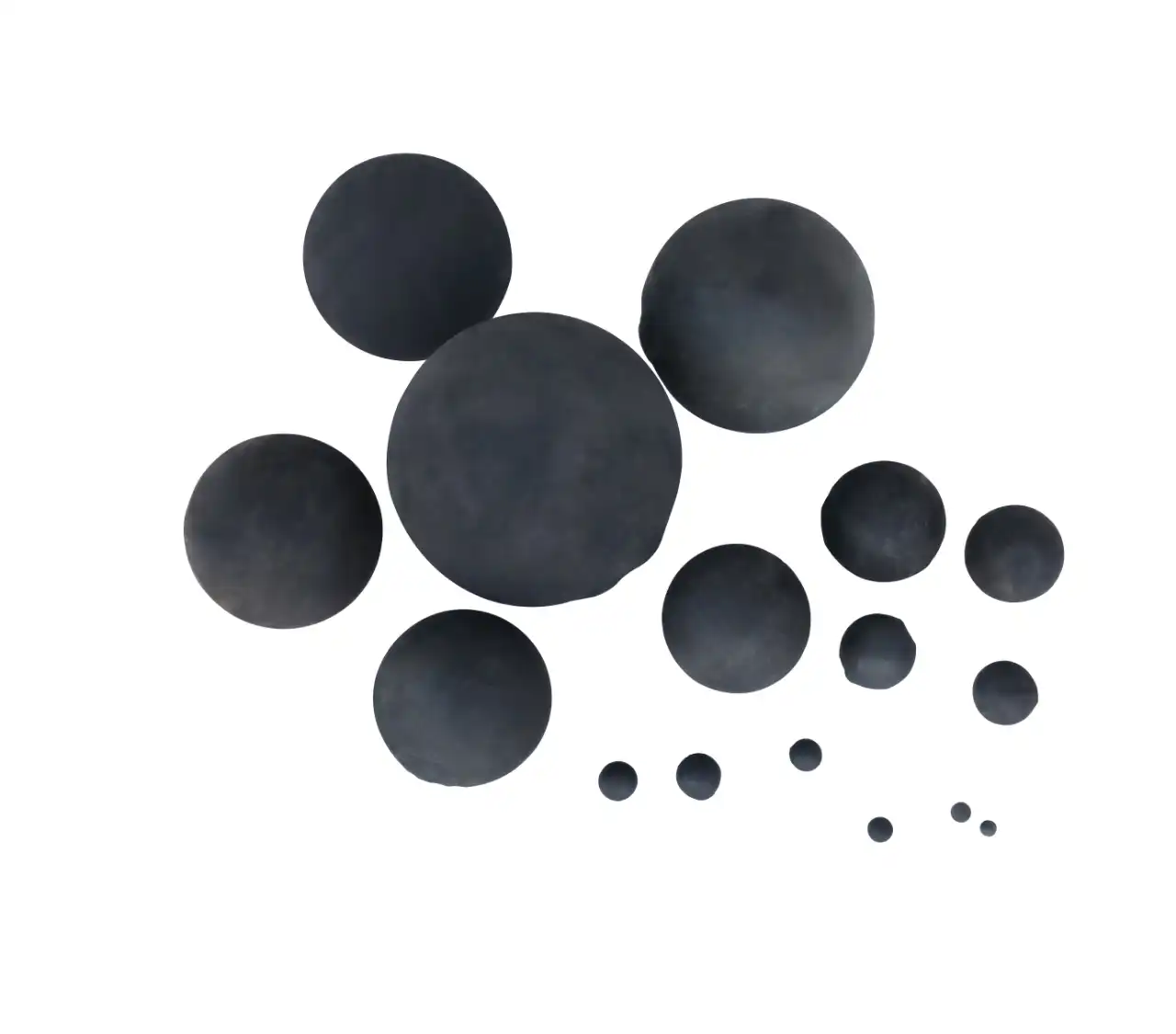
Grinding balls, particularly casting grinding balls, are essential components in various industrial processes. While their primary function is to crush and grind materials in mills, these versatile tools have found their way into some unexpected applications. In this article, we'll explore five creative ways to use grinding balls that you might not have considered before.